Reduced Duty Cycle Transformer Designs
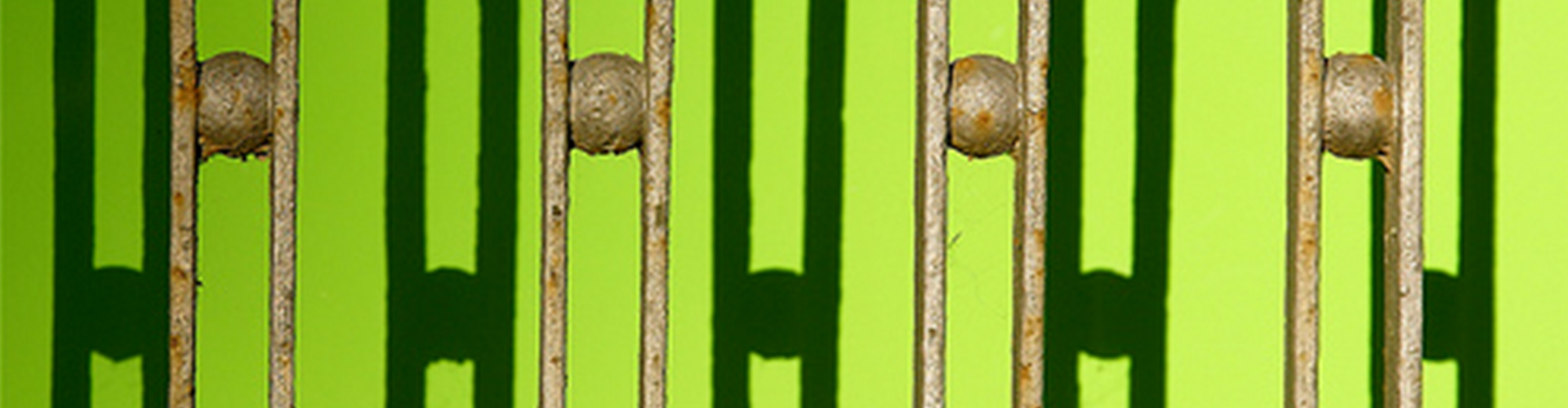
Image: Flickr user Toni F.
Designing transformers to take advantage of low duty cycle applications can save on physical size and potentially reduce the initial hardware investment. But this approach can quickly lead to component failures and loss of investment, particularly in cases when the specifying engineer miscalculates duty cycle.
1.) On-Off cycle must be considerably shorter than the thermal time constant of the transformer.
- Thermal time constants for transformers are usually expressed in hours.
- A 50 KVA, 100% duty cycle transformer has a thermal time constant of approximately 6-8 hours.
- If the On-Off cycle is less than 60 seconds, you can consider taking advantage of the reduced duty cycle approach in such a case.
2.) How to calculate Duty Cycle:
- Duty Cycle (As a Percent) = [Cycle On Time / (Cycle On Time + Cycle Off Time)] x 100
Example: On-Time = 6 seconds, Off-Time = 14 seconds, Duty Cycle = [6 / (6 + 14)] x 100 = 30 Percent
3.) How to Calculate Relative KVA size:
Relative KVA size is calculated by multiplying the 100% Duty Cycle KVA size by the square root of the duty cycle.
Example (Single Phase Application):
- Duty Cycle = 30.0 Percent
- Load during the On-Time = 50 KVA
- Therefore, Design KVA = 50 KVA x SQRT(0.300) = 50 x 0.548 = 27.4 KVA Design.
For easy calculation, assume the On-Time load is 100 Volts and 500 Amps (50 KVA).
- “Continuous” (100% DC) Design Current is 27.4 KVA / 100 Volts = 274.0 Amps.
A transformer designed to deliver a continuous current of 274.0 will perform well in an application designed to provide 500 Amps, operating at a 30.0 percent duty cycle.
Additional Issues to Consider
If a user is not aware of using a reduced duty cycle transformer, they may inadvertently increase the duty cycle beyond the capability of the transformer. We recently worked on a project involving an induction heating application that had been successfully running a 30 percent duty cycle transformer for many years. Unfortunately the project managers used this prior line as a model when designing a new production line with different specs. The machine user sought to increase productivity by reducing the duty cycle-times and thereby increasing the effective duty cycle. They increased the duty cycle 50 percent, and accidentally destroyed two power supply transformers before eventually identifying the root cause for the failure (duty cycle miscalculation).
Calculations illustrating the impact of the application are:
- Duty Cycle: 30 percent, On-time = 6 seconds, Off-time = 14 seconds
- “Actual” Duty Cycle: 50 percent, On-time = 6 seconds, Off-time = 6 seconds
- Design Equivalent Continuous Current (30% Duty) = 500 x SQRT(0.30) = 274.0 Amps
- Actual Equivalent Continuous Current (50% Duty) = 500 x SQRT(0.50) = 353.5 Amps
Since copper losses vary with the square of the current, running a transformer at 353.5 amps rather than 288.5 amps results in increased copper losses by (353.5 / 274.0)^2 = 1.66 times.
By increasing the power dissipated in the transformer windings by 1.66 times (66% increase), the result is typically an significantly overheated transformer. If the design temperature rise is 115 degrees Celsius, and the actual rise is 1.66 x 115 = 191 degrees Celsius, the life of the insulation system is seriously compromised.
A properly designed reduced duty cycle transformer can save size and money. Unfortunately we’ve seen a number of cases when specifying engineers make costly errors in calculating duty cycle. The results of a miscalculated duty cycle can lead to damaged equipment – effectively wasting more time and money than the engineers had hoped to save in the first place.
Let’s talk about your project.